1.精益生产培训费用:
¥3600元/人,3人以上团体报名9.5折优惠(含培训费、教材资料费、水果与茶点、午餐、培训证书、MINITAB软件、税费等)
费用不含培训期间的住宿费及其他个人消费(提供代订酒店服务)
2.精益生产培训形式:
公开课形式,所有课程可提供进厂培训,按课时收费,受训名额不限.
3.精益生产培训公开课计划:
2025年4月20-21日、5月19-20日、6月16-17日、7月15-16日、8月21-22日、9月20-21日、10月15-16日、11月19-20日、12月14-15日
杭州、上海、北京、广州四地滚动开班.
4.咨询电话
5.课程背景:
制造工厂一般面临品种多、更新快、产品质量要求高、生产流程长、工艺复杂等多重特点,而工厂厂车间是产品生产的重要场所,要保证产品的高质量、高效率、短周期、多快好省地生产出优良产品,就要从生产车间的各个环节的管理着手,严格对产品生产的每一个环节进行管理,优化产品生产的整个过程包括人、机、料、法、环、测等,是提高产品生产质量、提高生产效率、降低生产成本的关键所在,更是工厂最根本的责任表现。
但是,工厂的生产车间的各种因素又是极不稳定的和变化无常的,品种多、批量小、更新快、多以间歇方式进行的小批量生产。
随着工厂的竞争越来越激烈,如何能够快速生产出高品质、低成本、短交期以及符合客户需求的商品,是工厂迫在眉睫的能力要求。
而制造工厂的能力重点在哪里?毫无疑问,在产品的实现过程,即生产过程。
已有越来越多的制造工厂以精益生产方式为中心,以实现达成顾客交货要求的一切目标。
本课程是根据具有20余年工厂管理实践经验、原富士康科技集团精益管理研究院副院长、多家大型制造工厂主导精益生产改善咨询经验的精益管理专家段富辉老师在长期的生产一线中的管理实践、以及生产管理成功经验,结合精益生产管理理念,为制造工厂生产管理者提供的一套实用、实效、实战的精益管理思路、方案、方法与技巧。全国唯一,值得借鉴学习。
6.课程目标/收益:
通过学习学员能理解精益生产的发展历史。
剔除原有对精益认识的错误认识,建立精益新思想。
统一对精益生产作用和意义的认识,达成一致的行动意愿
掌握精益生产十大核心工具的使用方法,打造精益化的生产现场
帮助学员认清自己企业的七大浪费。
通过学习学员们能够认识现场管理与目视化管理。
通过学习使学员掌握准时化生产的要点和方法。
通过学习使学员掌握全方位的持续改善机制。
通过学习让学员坚持全方位变化,包括自身素养的变化。
7.课程对象:
生产经理、IE经理、精益工程师、厂长、工段长、车间主任、班组长等
8.授课方法:
理论讲授、数据分析、图片分享、工具介绍、工具演练、、分组讨论、、结果发布、讲师点评、持续改善计划。
9.精益生产培训课程大纲:
第一讲 精益基础篇
1.精益的形成
2.精益的发展
3.精益的定义
4.日本和德国的精益异同点
5.精益在我国大多数企业中为什么没有成功
案例分析:亲赴日本丰田研修带来的触动
案例分析:德国的工匠精神
第二讲:精益思想篇
1.何谓精益思想
2.精益思想的五大核心和五项原则
3.精益思想形成的四大步骤
4.如何使精益思想贯彻始终
案例分享:精益是一种职业病
第三讲:精益要消除的七种浪费
1.库存的浪费产生的根源及治理方法
2.生产过多/过早的浪费产生产根源及治理方法
3.过度加工的浪费产生的根源及治理方法
4.搬运的浪费产生的根源及治理方法
5.等待的浪费产生的根源及治理方法
6.动作的浪费产生的根源及治理方法
7.质量不良的浪费产生的根源及治理方法
案例:某工厂现场改善的价值
第四讲:精益10工具解析
工具1- VSM价值流图析
1)何谓VSM价值流图析
2)价值流图说明与数据采集
3)确定产品系列
4)绘制当前状态图
5)价值流现状分析
6)绘制未来状态图
7)设定改善目标
8)制定改善计划
案例分析:某电子组装厂推行VSM是如何将生产周期从15天缩短为10天的?
工具2-问题分析与解决
1)何谓问题
2)丰田问题解决方式TBP
3)戴明环PDCA
4)七何法(5W2H)
5)五个为什么(5Why)
6)脑力风暴
7)快速响应
8)异常管理
9)8D报告
案例分析:某工厂《改善报告》
工具3-现场5S管理
1)1.5S的基本概念
2)2.5S的作用和意义
3)3.5S推进重点
4)4.5S案例展示
5)5.传统5S与精益5S的对比说明
6)6.5S督查机制
案例分析:推行6S失败的原因
工具4-可视化管理
1)可视化管理原理
2)周期性信息展示
3)3、3M的实时监控
4)基于“三现主义”的异常管理
5)可视话化管理的三级基准
案例分析:可视化管理为什么成为了形式?
工具5-标准化作业
1)何谓标准化作业
2)标准化作业的四大前提条件
3)作业分类
4)标准化作业三要素(TT,WS,SWIP)
5)标准化作业三件套
6)标准化作业的应用
7)标准化作业的管理
8)标准化作业的改善
9)标准化作业对产品质量的改进意义
案例分析:企业的标准化为什么成为了两张皮?
工具6-现场IE改善
1)维持、改善与创新
2)现场IE改善体系架构
3)现场中心
4)改善步骤
5)ECRS四则
6)现场IE改善的七大手法
7)自主改善
案例分析:某工厂包装车间如何通过IE改善提升生产效率25%的?
工具7-全员生产维护(TPM)
1)TPM的概念和目的
2)设备综合效率(OEE)
3)如何进行个别改善
4)故障时间与故障修复时间
5)自主维护保养
6)如何开展小组活动
7)如何开展六源法
8)如何识别微小缺陷
案例分析:某铝板压轧车间如何通过TPM提升设备效率15%的?
工具8-快速换产
1)何谓快速换产(换型/换模/换线)
2)快速换型与均衡生产
3)SMED的基本原理
4)SMED的基本要点
5)SMED的五步操作法
6)快速换产(换型/换模/换线)的效果评估
7)快速换产(换型/换模/换线)案例分析
案例分析:某铝铂车间是如何通过快速换产提高生产效率增加员工计件工资的?
工具9-防错技术
1)追求零缺陷
2)失误与缺陷
3)品质三不政策
4)防错三个等级
5)防错十大原理
6)防错装置
案例分析:来自生活中的防错手法
工具10-看板拉动
1)拉动式与推动式生产的区别
2)看板起源与作用
3)看板的种类与工作原理
4)看板的实施前提
5)看板运行的六原则
6)看板数量计算
7)看板运行注意事项
案例分析:某电子产品车间通过单件流的看板拉动生产方式
第五讲:成功导入精益生产的关键条件
1.领导参与
2.员工认同
3.制定规则
4.取得支持
5.依赖数据
6.培养员工
7.庆祝成功
8.持续改进
案例分析:为什么领导才是决定推行成功的关键
课程总结:提问、答疑
10.精益生产培训心得:
很荣幸参加Ralap举办的精益生产培训,虽然只有短短几天时间,但是老师深入浅出的讲解,详实的案例研讨,以学员为中心、与学员相互交流的培训理念,使得我收益颇多。让我了解精益生产的起源和本质,浪费的7+X模式,准时生产与精益生产的关系,看板控制、拉式系统和准时生产的逻辑,还有丰田生产方式的精髓
-
精益生产的起源和本质
精益生产(Lean Production,LP)是二战后日本汽车工业遭到“资源短缺”和面临“多品种、少批量”的市场制约的产物,因日本丰田汽车公司从一个不起眼的小公司发展成为世界最大的汽车制造商,而引起人们关注,丰田汽车公司创立的“丰田生产体系(Toyota Production System,TPS)”是精细生产的核心。
精益生产是强调精打细算,使资源消耗最少的一种生产哲理和生产方式,它包括一系列通过消除浪费的简化过程来降低成本的原理和实践。精益生产系统以一个中心,2个主柱,一种土壤为核心构成,,如下图所示:
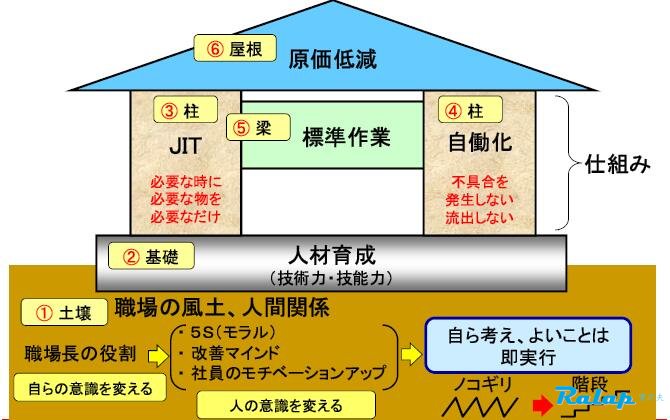
............
11.精益生产培训课程案例: